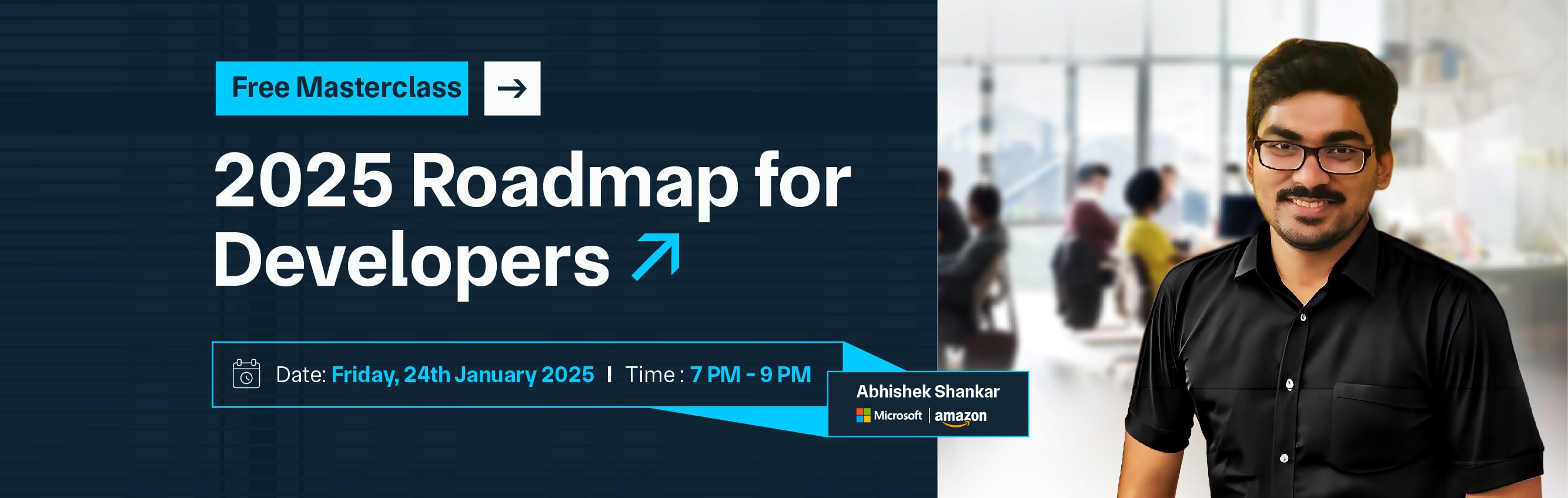
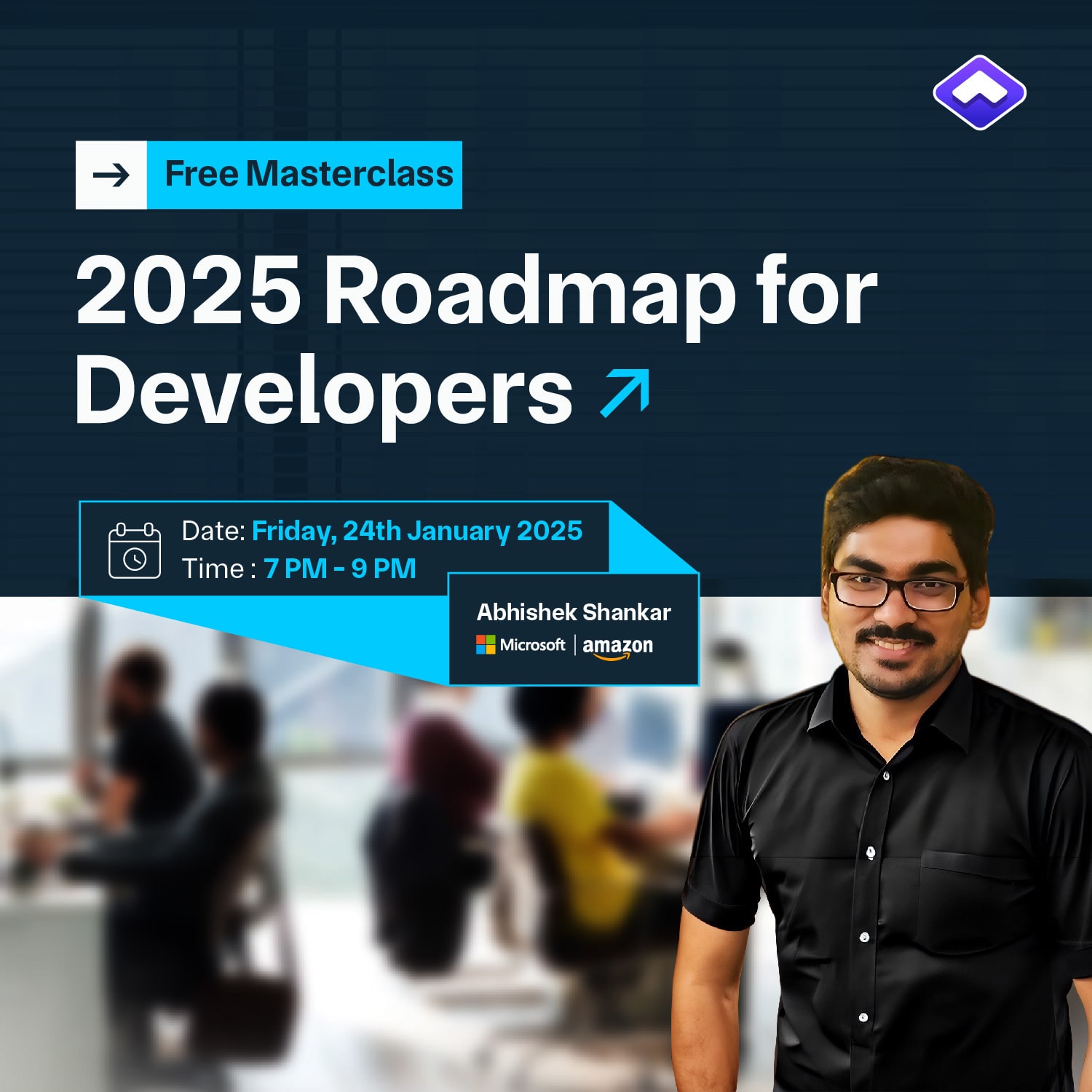
The Six Sigma DMADV methodology, standing for Define, Measure, Analyze, Design, and Verify, is a structured approach used to design or redesign processes, products, or services to meet Six Sigma quality standards. This methodology is crucial for organizations aiming to achieve high performance and efficiency by eliminating defects and ensuring quality in the final outputs. Unlike DMAIC (Define, Measure, Analyze, Improve, Control), which focuses on improving existing processes, DMADV is specifically tailored for creating new processes or products from the ground up.
In the DMADV approach, the first phase, Define, involves identifying the project goals, customer requirements, and deliverables. This phase sets the direction for the entire project, ensuring alignment with the organization’s strategic objectives and customer expectations. The measure follows, where teams collect data on current capabilities and define metrics for the new design, ensuring that all relevant factors are considered.
Analyze involves evaluating data to identify potential design solutions that meet the defined requirements. The Design phase then develops these solutions into detailed designs or prototypes, incorporating feedback and iterations as necessary. Finally, Verify involves testing the new design to ensure it meets the initial goals and performs as expected in real-world conditions. By rigorously applying these stages, the DMADV methodology ensures the development of robust and effective solutions that drive organizational success.
Six Sigma is a data-driven methodology designed to improve the quality and efficiency of processes by identifying and eliminating defects and variations. Originating from the manufacturing sector, it has since been applied across various industries.
The core principle of Six Sigma is to reduce process variation to achieve a level of performance that results in no more than 3.4 defects per million opportunities. This goal is achieved through a rigorous approach that involves defining, measuring, analyzing, improving, and controlling processes to enhance overall quality. The Six Sigma framework uses a variety of tools and techniques, including statistical analysis and process mapping, to achieve its objectives.
It emphasizes the importance of leadership and a structured approach to problem-solving, often involving specialized roles such as Green Belts and Black Belts, who are trained in Six Sigma methodologies. By focusing on data-driven decision-making and continuous improvement, Six Sigma helps organizations enhance their operational efficiency, improve customer satisfaction, and gain a competitive edge in the market.
DMADV is a Six Sigma methodology designed specifically for developing new processes, products, or services that adhere to high-quality standards. DMADV stands for Define, Measure, Analyze, Design, and Verify. Unlike the DMAIC methodology, which is focused on enhancing existing processes, DMADV is utilized for creating new solutions from the ground up.
The primary objective of DMADV is to ensure that new designs meet customer needs and organizational goals while maintaining Six Sigma quality levels. By following these structured steps, organizations can craft solutions that are not only effective and efficient but also aligned with their strategic goals and deliver superior performance.
The Define phase is the foundational step in the DMADV process, where the project’s goals, customer requirements, and scope are established. This involves a comprehensive understanding of the problem, setting clear and measurable objectives, and identifying all relevant stakeholders.
It is essential to define the project in a way that aligns with customer needs and organizational strategies, ensuring that all parties involved have a clear understanding of the project’s direction and expected outcomes.
In the Measure phase, the focus shifts to gathering data and defining metrics to evaluate the new design's performance. This includes identifying key performance indicators (KPIs) that are crucial for assessing the design’s effectiveness.
Establishing benchmarks and collecting relevant data is critical to understanding how well the proposed solution meets the project requirements. Accurate measurement is essential for making informed decisions and ensuring that the new design performs as intended.
The Analyze phase involves using the data collected during the Measure phase to explore potential solutions. This step includes evaluating different design options, assessing their feasibility, and predicting their performance based on the gathered data.
The goal is to identify the most effective design that meets the defined requirements and delivers the desired results. Analysis involves rigorous evaluation and comparison of various solutions to determine the best fit for the project.
In the Design phase, the selected solution is developed into a detailed design or prototype. This includes creating comprehensive specifications, conducting simulations, and performing tests to refine the design based on feedback.
The objective is to ensure that the design not only meets all requirements but also performs effectively in real-world conditions. Iterative testing and refinement help to address any issues and enhance the design’s performance before full-scale implementation.
The Verify phase focuses on validating the final design through testing and real-world implementation. This step involves pilot runs or full-scale deployment to ensure that the design meets the project goals and customer requirements.
Verification includes making necessary adjustments based on feedback and performance data to ensure that the solution delivers the expected results. This phase is critical for confirming that the new design achieves its intended objectives and provides the desired benefits.
DMADV is an advanced Six Sigma methodology designed for projects that involve the creation of new processes, products, or services. It is particularly useful when existing solutions are inadequate or when there is a need for innovative and high-quality designs.
This methodology ensures that the new solutions meet customer requirements, achieve high-performance standards, and align with organizational goals. By following the structured approach of DMADV, organizations can develop solutions that are robust, effective, and capable of delivering exceptional results.
When launching a new product, DMADV provides a systematic framework to ensure that the product meets high-quality standards and customer expectations. This methodology begins with defining customer needs and project goals, followed by measuring relevant performance metrics and analyzing potential design options. In the Design phase, a detailed prototype is created and tested to ensure it fulfills all requirements.
The final Verify phase involves rigorous testing and validation to confirm that the product performs as intended and delivers the expected value to customers. This comprehensive approach minimizes risks and ensures a successful product launch.
For organizations looking to establish new processes, DMADV offers a structured approach to ensure efficiency and effectiveness. The methodology starts with defining the objectives and scope of the new process, identifying the key performance indicators, and measuring their potential impact. During the Analyze phase, different process designs are evaluated to determine the best option.
The Design phase involves developing a detailed process framework, followed by the Verify phase, where the new process is tested to ensure it operates smoothly and meets all performance standards. This approach helps in creating streamlined processes that align with business goals and improve operational efficiency.
When introducing new services, DMADV helps design solutions that meet customer needs and high-quality standards. The methodology begins with defining the service requirements and customer expectations, measuring the critical service performance metrics, and analyzing different service design options. The Design phase involves creating a detailed service model or prototype.
In contrast, the Verify phase includes testing the service in real-world conditions to ensure it meets all customer requirements and delivers the desired outcomes. This approach ensures that the new service is both innovative and effective, enhancing customer satisfaction and achieving business objectives.
DMADV is also useful when significant design changes are needed for existing products or processes. This methodology helps in defining the scope of the changes, setting clear objectives, and measuring the impact of the redesign. During the Analyze phase, various design alternatives are evaluated to select the best solution.
The Design phase focuses on developing a detailed redesign, and the Verify phase involves testing the new design to ensure it meets all criteria and performs as expected. This approach ensures that major changes are implemented effectively, improving the overall performance and quality of the existing solution.
When achieving Six Sigma quality levels is crucial, DMADV provides a robust framework to ensure that new designs meet the highest quality standards. The methodology begins with defining quality requirements and metrics, measuring their impact, and analyzing design options to meet these standards.
In the Design phase, a detailed solution is developed and refined, followed by the Verify phase, where the solution is tested to confirm it meets all quality benchmarks. This approach ensures that the final solution consistently delivers exceptional performance and reliability, aligning with rigorous quality expectations.
DMADV, a Six Sigma methodology, offers several advantages for designing new processes, products, or services that meet high-quality standards. This approach provides a structured framework for ensuring that new designs align with customer needs and organizational goals.
By emphasizing thorough analysis and validation, DMADV helps mitigate risks associated with new developments and enhances the likelihood of successful outcomes. Its focus on quality and performance from the outset leads to more effective and reliable solutions, ultimately contributing to improved customer satisfaction and business success.
DMADV is widely used across various industries to design new products, services, and processes that meet high standards of quality and performance. By providing a structured approach, DMADV helps organizations create solutions that are both effective and aligned with customer needs.
Real-world examples illustrate how this methodology can be applied to diverse scenarios, showcasing its versatility and effectiveness in delivering innovative and high-quality outcomes.
DMADV and DMAIC are both Six Sigma methodologies but serve distinct purposes. While DMADV focuses on designing new processes, products, or services to meet high-quality standards, DMAIC is used for improving existing processes that are already in place.
Understanding their differences is crucial for selecting the appropriate methodology based on the project requirements—whether the goal is to innovate and design or to optimize and enhance existing systems.
In addition to DMADV, various other methodologies within Design for Six Sigma (DFSS) provide structured approaches to achieving high-quality designs and processes. Each method addresses unique design challenges, ensuring that new products and processes meet customer requirements and Six Sigma standards.
Understanding these methodologies helps organizations select the most appropriate approach for their specific needs, enhancing the effectiveness and quality of their design efforts.
IDOV is a DFSS methodology that emphasizes a comprehensive approach to designing new processes or products. It starts with Identify, where the problem or opportunity is defined, and customer requirements are gathered. The Design phase involves developing detailed specifications based on these requirements.
Optimize focuses on refining the design by evaluating and enhancing its performance. Finally, Validate tests the design in real-world conditions to ensure it meets all requirements and performs as expected. This structured process helps ensure robust and effective design outcomes.
Design for Six Sigma (DFSS) is a broad methodology that encompasses various approaches to designing new processes and products with Six Sigma quality. The focus is on integrating Six Sigma principles into the design phase to ensure high-quality outcomes from the outset.
The application involves using different tools and techniques tailored to specific design needs. Tools include statistical analysis, design validation, and quality management techniques that support effective and efficient design processes. DFSS ensures that new designs meet customer needs and achieve performance excellence.
DMADV is a specific DFSS methodology used for creating new processes or products that meet Six Sigma quality standards. The focus is on a structured approach, beginning with Define, where project goals and customer requirements are established.
The measure involves collecting data and defining metrics for evaluating the design. Analyze uses data to identify potential solutions and assess their feasibility. Design develops the chosen solution into a detailed design or prototype. Finally, Verify tests the design to ensure it meets requirements and performs as expected.
DMADV (Define, Measure, Analyze, Design, Verify) utilizes a variety of tools and techniques to ensure that new processes or products are designed to meet high-quality standards. These tools support each phase of the methodology, from defining project goals to verifying the final design.
By leveraging these techniques, organizations can systematically address design challenges, optimize performance, and achieve Six Sigma quality in their new solutions. Each tool is selected based on its ability to address specific aspects of the design process, helping to ensure comprehensive and effective outcomes.
Implementing DMADV (Define, Measure, Analyze, Design, Verify) methodology can present several complex challenges that impact the overall effectiveness of the process. These challenges often arise from difficulties in defining clear project objectives, ensuring accurate data collection, and achieving stakeholder alignment.
Additionally, the complexity involved in analyzing data, managing design changes, and validating the final output can create obstacles. Addressing these challenges requires a strategic approach, advanced tools, and effective communication to ensure successful project outcomes. Overcoming these hurdles is crucial for developing high-quality designs that meet customer expectations and organizational goals.
Training and certification in DMADV (Define, Measure, Analyze, Design, Verify) are essential for professionals aiming to implement this Six Sigma methodology effectively. Such programs provide comprehensive knowledge of the DMADV process, tools, and techniques necessary for successful project execution. Certification demonstrates proficiency in applying DMADV principles and is valuable for career advancement in quality management and process improvement.
Various training options and certification levels are available to cater to different experience levels and professional needs, ensuring that individuals and organizations can achieve their quality goals efficiently.
The future of DMADV (Define, Measure, Analyze, Design, Verify) in business processes is promising, with increasing emphasis on innovation and quality management. As organizations strive to meet evolving customer expectations and adapt to technological advancements, DMADV provides a structured approach to developing new, high-quality processes and products.
Its relevance is growing in industries focused on designing cutting-edge solutions and achieving competitive advantages. The continuous evolution of digital tools and data analytics will further enhance the effectiveness of DMADV, making it a vital methodology for future business process improvements.
Six Sigma is a data-driven methodology aimed at improving business processes by identifying and eliminating defects and variability. Its core principles focus on achieving high levels of quality and efficiency through rigorous analysis and continuous improvement.
By adhering to these principles, organizations can enhance performance, reduce errors, and increase customer satisfaction. Understanding and applying the key principles of Six Sigma enables businesses to streamline operations and achieve operational excellence, aligning process improvements with strategic goals.
Six Sigma places a strong emphasis on understanding and meeting customer needs. By defining quality from the customer’s perspective, organizations ensure that their products and services deliver real value and satisfaction.
This customer-centric approach drives process improvements that align with customer expectations, enhancing overall experience and fostering long-term loyalty. Ensuring that customer feedback is consistently incorporated into process designs helps businesses stay competitive and responsive to market demands.
Data-driven decision-making is a cornerstone of Six Sigma. Instead of relying on intuition or guesswork, Six Sigma uses statistical analysis and data collection to guide decisions.
This approach involves gathering relevant data, analyzing it to uncover insights, and using these insights to address problems and implement improvements. By grounding decisions in empirical evidence, organizations can make more informed choices that lead to measurable and sustainable improvements, thereby reducing errors and enhancing process efficiency.
Continuous improvement is a key principle of Six Sigma, driving organizations to seek ways to enhance processes and reduce defects consistently. This principle is embodied in methodologies such as DMAIC (Define, Measure, Analyze, Improve, Control) and DMADV (Define, Measure, Analyze, Design, Verify), which provide structured approaches to problem-solving and process optimization.
By embracing a culture of ongoing improvement, organizations can achieve incremental gains that accumulate over time, leading to significant enhancements in performance and quality.
Employee involvement and empowerment are crucial for the success of Six Sigma initiatives. The methodology encourages engaging employees at all levels in problem-solving and decision-making processes.
By fostering a collaborative environment where team members are encouraged to contribute ideas and participate in improvement activities, organizations can leverage diverse perspectives and expertise. Empowering employees not only enhances their commitment to the process but also drives innovation and facilitates the effective implementation of improvement strategies.
Rigorous process analysis is integral to Six Sigma, involving a thorough examination of processes to identify inefficiencies and areas for improvement. Techniques such as process mapping, root cause analysis, and failure mode effects analysis (FMEA) are employed to understand process dynamics, pinpoint issues, and develop effective solutions.
By systematically analyzing processes, organizations can uncover underlying problems, optimize performance, and achieve higher levels of consistency and quality in their operations.
Standardizing best practices ensures consistency and quality across an organization. Six Sigma promotes the development and implementation of standardized procedures and guidelines based on successful improvement initiatives.
By codifying best practices and ensuring they are consistently applied, organizations can maintain high standards of performance and quality. Standardization not only helps in sustaining improvements but also facilitates efficient training and reduces variability, leading to more predictable and reliable outcomes.
Six Sigma is a data-driven methodology aimed at enhancing the quality of processes by identifying and eliminating defects and variability. It focuses on achieving a high level of precision and consistency, with the goal of reducing process variation to improve overall performance. The methodology uses statistical tools and techniques to analyze processes, identify areas of improvement, and implement solutions that lead to measurable enhancements in efficiency and quality.
By adhering to Six Sigma principles, organizations can minimize errors, reduce costs, and increase customer satisfaction through rigorous process optimization. The Six Sigma methodology is structured around two primary frameworks: DMAIC and DMADV. DMAIC (Define, Measure, Analyze, Improve, Control) is used for improving existing processes, focusing on identifying defects and implementing corrective actions.
DMADV (Define, Measure, Analyze, Design, Verify) is employed for designing new processes or products, ensuring that they meet high-quality standards from the outset. Both frameworks rely on data analysis and statistical methods to drive continuous improvement and maintain high levels of process excellence. By integrating Six Sigma into their operations, organizations can achieve sustainable performance improvements and align their processes with strategic business goals.
Six Sigma techniques are methodologies and tools used to improve process quality by identifying and eliminating defects and variations. These techniques are grounded in statistical analysis and data-driven decision-making, focusing on achieving high levels of performance and efficiency.
By employing these techniques, organizations can systematically address process inefficiencies, enhance product quality, and drive continuous improvement. Here are some key Six Sigma techniques:
Six Sigma tools are essential instruments used to analyze, measure, and improve processes by identifying defects and inefficiencies. These tools provide structured approaches to problem-solving and process enhancement, leveraging statistical analysis and data-driven methods. By utilizing these tools, organizations can achieve greater consistency, quality, and efficiency in their operations. Here are some key Six Sigma tools:
Six Sigma levels refer to the different stages of quality improvement within an organization, each representing a specific degree of process performance and proficiency. These levels are categorized based on the defect rates and the extent of process optimization achieved. Achieving higher Six Sigma levels indicates a more refined and effective approach to quality management. Here are the key Six Sigma levels:
DMADV (Define, Measure, Analyze, Design, Verify) is a crucial methodology in Six Sigma designed for developing new processes, products, or services with a focus on achieving high-quality standards from the outset. Unlike DMAIC, which is used for improving existing processes, DMADV is employed when creating entirely new designs or systems, ensuring that they meet or exceed customer expectations and organizational goals. The methodology’s structured approach guides teams through a comprehensive process, starting with defining the project’s objectives and customer requirements.
It then involves measuring and analyzing data to inform the design phase, followed by rigorous verification to ensure the final design performs as intended. By adhering to the DMADV framework, organizations can enhance their ability to deliver innovative solutions that align with strategic objectives and maintain Six Sigma quality levels. This proactive approach not only helps in meeting customer needs but also positions businesses for long-term success through effective and efficient design processes.
Copy and paste below code to page Head section
DMADV stands for Define, Measure, Analyze, Design, and Verify. It is a Six Sigma methodology specifically used for designing new processes, products, or services to meet high-quality standards and customer requirements. This structured approach ensures that new designs are effective, meet organizational goals, and align with customer needs from the outset.
DMADV is used for creating new processes or products, whereas DMAIC focuses on improving existing ones. DMAIC is applied when addressing inefficiencies or defects in current systems, while DMADV aims to design and implement solutions from scratch, ensuring they meet high-quality standards from the beginning.
DMADV should be employed when developing new products, processes, or services where existing solutions are inadequate or when there is no existing process. It ensures that the new designs are robust, efficient, and meet customer requirements, reducing the risk of defects and inefficiencies.
The key phases are Define (establish goals and requirements), Measure (collect data and define metrics), Analyze (evaluate design options), Design (develop and refine the solution), and Verify (test and validate the final design). Each phase builds on the previous one to ensure the outcome meets all specifications.
Common tools include Voice of the Customer (VOC) for capturing requirements, Failure Mode and Effects Analysis (FMEA) for assessing potential failures, Design of Experiments (DOE) for testing variables, and Pilot Testing for validating the final design. These tools help ensure the new design meets quality and performance standards.
In the Define phase, the project's goals, customer requirements, and scope are clearly outlined. This phase involves identifying the problem, setting objectives, and understanding stakeholder needs to ensure that the project aligns with customer expectations and organizational strategies.