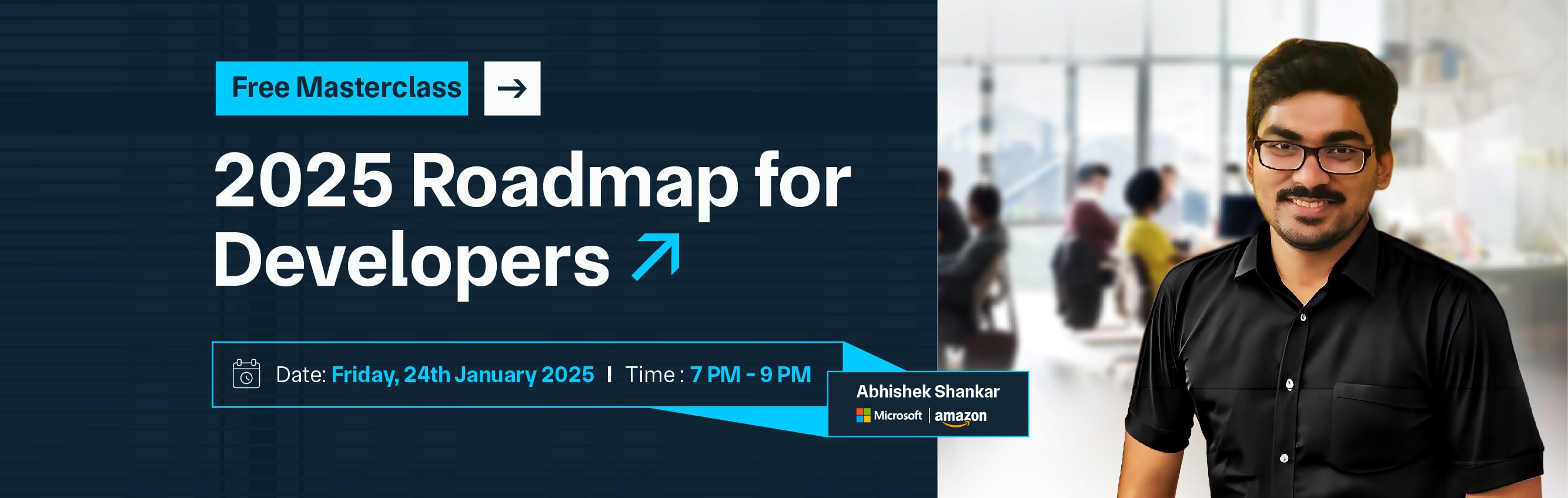
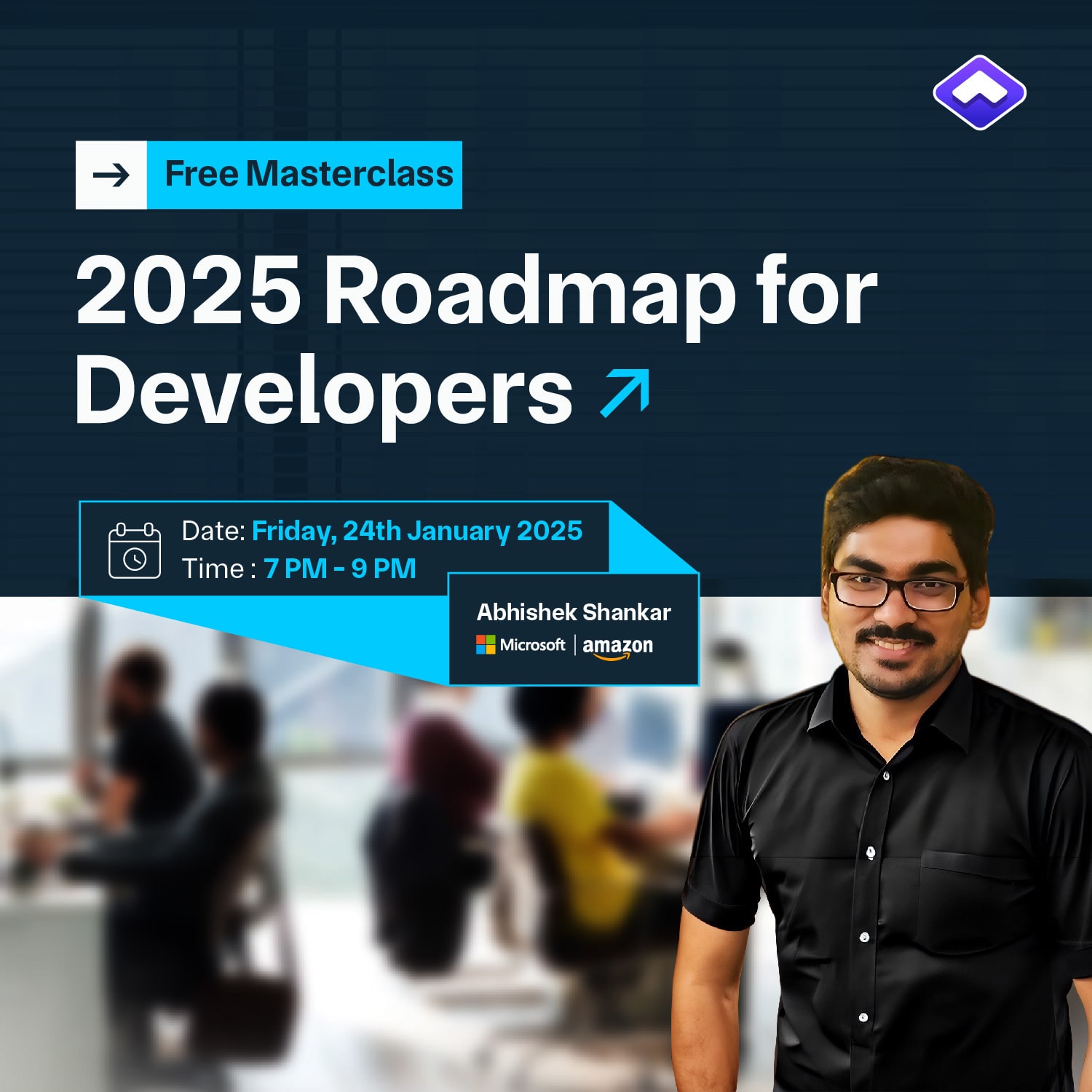
Six Sigma is a data-driven methodology used in operations management to improve processes by eliminating defects and reducing variability. Originating from Motorola in the 1980s, Six Sigma focuses on enhancing process efficiency and effectiveness through a rigorous framework. Its primary goal is to achieve near-perfect quality by identifying and addressing sources of errors within operational processes. The methodology utilizes statistical tools and techniques to measure performance, identify problems, and implement solutions that drive improvements. In operations management, Six Sigma is implemented through a structured approach that includes defining, measuring, analyzing, improving, and controlling processes.
This approach, known as DMAIC, helps organizations systematically address inefficiencies and improve overall performance. By applying Six Sigma principles, businesses can streamline their operations, reduce waste, and enhance customer satisfaction. The methodology's emphasis on data-driven decision-making ensures that improvements are based on empirical evidence rather than intuition.
The adoption of Six Sigma in operations management can lead to significant benefits, including cost savings, improved quality, and increased productivity. Organizations that embrace Six Sigma often experience enhanced competitive advantage due to their ability to deliver high-quality products and services consistently. By fostering a culture of continuous improvement, Six Sigma empowers teams to address challenges and drive sustainable growth proactively.
Six Sigma is a systematic approach used in operations management to enhance process quality by identifying and eliminating defects. Originating in the 1980s, Six Sigma aims to improve operational efficiency and reduce variability by employing statistical methods. The core idea is to achieve near-perfect performance by minimizing errors and deviations in processes.
This methodology involves using data-driven techniques to measure and analyze performance, ensuring that improvements are based on solid evidence rather than guesswork. In practice, Six Sigma is applied through a structured framework known as DMAIC, which stands for Define, Measure, Analyze, Improve, and Control.
This process helps organizations identify the root causes of inefficiencies, implement solutions, and maintain improvements over time. By focusing on reducing defects to fewer than 3.4 per million opportunities, Six Sigma helps businesses enhance their processes, reduce costs, and improve customer satisfaction.
Six Sigma principles are designed to drive operational excellence by improving process quality and efficiency. These principles provide a structured approach to identifying and eliminating defects, reducing variability, and enhancing performance. By leveraging statistical analysis and data-driven methods, Six Sigma helps organizations achieve higher levels of consistency and customer satisfaction.
The principles emphasize a continuous improvement mindset and the importance of using empirical evidence to guide decision-making. Here’s a closer look at the key Six Sigma principles that guide operations improvement.
Establishing clear objectives and metrics is essential for guiding process improvements and evaluating success. Clearly defined goals align activities with strategic priorities and provide a benchmark for performance assessment. Setting measurable metrics enables organizations to track progress, identify areas for improvement, and ensure that objectives are met.
This clarity helps in focusing efforts on achieving specific outcomes and facilitates effective performance management. By having well-defined objectives and metrics, organizations can make informed decisions and drive continuous progress toward operational excellence.
Data-driven decision-making is central to optimizing operations management. By leveraging data, organizations can make informed decisions based on objective evidence rather than relying on assumptions. The process involves collecting and analyzing relevant performance metrics to identify trends, uncover underlying issues, and evaluate the effectiveness of changes.
This approach allows for precise adjustments to be made, improving process efficiency and effectiveness. Data-driven decisions ensure that improvements are targeted and measurable, leading to better outcomes and continuous enhancement of operational performance.
Cross-functional collaboration is a cornerstone of effective operations management. It involves fostering teamwork and communication across different departments and functions to ensure that all perspectives are considered. By breaking down silos and encouraging open dialogue, organizations can streamline processes and address issues more comprehensively.
This collaborative approach ensures that solutions are well-rounded and integrated, leading to more efficient operations and improved overall performance. Effective cross-functional collaboration enhances problem-solving and innovation, contributing to a more cohesive and agile organization.
Continuous improvement is vital for maintaining high-performance levels in operations management. This principle involves regularly assessing processes to identify areas for enhancement and making iterative changes. By adopting a mindset of ongoing evaluation and adjustment, organizations can adapt to evolving needs and challenges.
Continuous improvement fosters a culture of innovation and responsiveness, enabling organizations to stay competitive and efficient. Regularly revisiting and refining processes helps in achieving long-term success and operational excellence, ensuring that improvements are sustained and performance remains high.
Integrating technology and automation into operations management can significantly boost efficiency and accuracy. Automation tools reduce manual effort and minimize errors by streamlining repetitive tasks and processes. Leveraging advanced technologies improves workflow management, data accuracy, and processing speed, which in turn accelerates overall operational performance.
By incorporating these tools, organizations can achieve faster turnaround times and enhance operational excellence. The use of technology not only optimizes existing processes but also supports the development of innovative solutions and improvements.
Establishing clear objectives and metrics is essential for guiding process improvements and evaluating success. Clearly defined goals align activities with strategic priorities and provide a benchmark for performance assessment. Setting measurable metrics enables organizations to track progress, identify areas for improvement, and ensure that objectives are met.
This clarity helps in focusing efforts on achieving specific outcomes and facilitates effective performance management. By having well-defined objectives and metrics, organizations can make informed decisions and drive continuous progress toward operational excellence.
Investing in employee training and development is crucial for enhancing operational efficiency and effectiveness. Well-trained staff are better equipped to handle their roles, identify issues, and implement solutions effectively. Ongoing development opportunities help employees stay current with industry trends and best practices.
This investment in skills and knowledge fosters a culture of continuous learning and improvement. By supporting employee growth, organizations not only enhance individual performance but also contribute to overall process improvements and operational success.
Quality control is fundamental to ensuring high standards and preventing defects in operations management. This involves establishing clear quality standards, conducting regular inspections, and using feedback to make necessary adjustments. Robust quality control measures help in maintaining consistency and meeting customer expectations.
By prioritizing quality control, organizations can detect and address issues early, reducing the risk of defects and ensuring compliance with regulatory requirements. Effective quality control contributes to improved product and service quality, leading to enhanced customer satisfaction and operational efficiency.
Six Sigma is a critical methodology in operations management that focuses on improving process quality and efficiency by identifying and eliminating defects. By using data-driven approaches, Six Sigma helps organizations achieve high levels of performance and customer satisfaction.
Its systematic methodology enhances operational efficiency, reduces costs, and promotes continuous improvement. Implementing Six Sigma principles enables businesses to streamline processes, ensure consistent quality, and maintain a competitive edge in the market.
Six Sigma approaches are crucial for systematically enhancing operational efficiency and effectiveness by addressing process deficiencies and minimizing variations. These methodologies provide a structured framework to identify, analyze, and improve processes, leading to substantial improvements in quality and performance. Here are the key steps involved:
By following these Six Sigma approaches, organizations can systematically improve their processes, enhance quality, and achieve operational excellence.
Six Sigma tools are critical for driving process improvements and ensuring operational excellence. These tools provide structured methodologies for identifying problems, analyzing data, and implementing effective solutions.
By applying Six Sigma tools, organizations can systematically reduce variability, enhance quality, and achieve more efficient and predictable outcomes. These tools are designed to support various stages of the Six Sigma methodology, including defining problems, measuring performance, analyzing data, and controlling processes.
Six Sigma offers a range of tools designed to support various aspects of process improvement and quality management. These tools help organizations analyze data, identify issues, and implement effective solutions.
By leveraging these tools, companies can achieve better control over their processes, enhance efficiency, and improve overall performance. Each tool provides unique insights and aids in different stages of the Six Sigma methodology, from initial analysis to long-term control.
Implementing Six Sigma initiatives in operations management involves a structured approach to enhancing process efficiency and quality. The process begins with defining the problem areas and setting clear objectives aligned with organizational goals. This involves using Six Sigma methodologies, such as DMAIC (Define, Measure, Analyze, Improve, Control), to systematically identify performance gaps, measure current capabilities, analyze root causes, and implement targeted improvements.
By applying statistical analysis and data-driven techniques, organizations can address defects, reduce process variability, and optimize workflows. Successful implementation requires a commitment to continuous improvement and the involvement of cross-functional teams to ensure that changes are effectively integrated into existing processes. In addition to process improvements, Six Sigma initiatives focus on fostering a culture of quality and accountability.
This involves training employees in Six Sigma principles and tools, encouraging their active participation in improvement projects, and establishing clear metrics to monitor progress. Regular reviews and adjustments are necessary to sustain the gains achieved and adapt to evolving business needs. By embedding Six Sigma into the organizational culture, companies can drive sustained operational excellence, enhance customer satisfaction, and achieve competitive advantages in the marketplace.
Six Sigma has been successfully implemented across various industries to enhance operational efficiency and improve quality. Real-life use cases demonstrate how Six Sigma methodologies can address complex challenges, streamline processes, and deliver significant results.
By applying Six Sigma tools and techniques, organizations can identify and eliminate inefficiencies, reduce defects, and achieve measurable improvements in performance. These case studies highlight the practical applications of Six Sigma principles in driving operational excellence and achieving business goals.
In the manufacturing industry, Six Sigma has played a crucial role in reducing defects and improving product quality. General Electric (GE) implemented Six Sigma to address defect rates in its manufacturing processes. Through the DMAIC methodology, GE identified that inconsistencies in raw materials and process variations primarily caused defects.
By implementing corrective actions and process improvements, GE achieved a 60% reduction in defect rates, saving the company approximately $500 million annually. This significant decrease in defects not only cut costs but also enhanced product reliability, leading to improved customer satisfaction.
In the healthcare sector, Six Sigma has been instrumental in improving patient care and operational efficiency. A major hospital chain utilized Six Sigma to streamline its patient discharge process, which was previously causing delays. The hospital applied Six Sigma tools to identify bottlenecks and inefficiencies, such as delays in paperwork and communication.
By addressing these issues, the hospital reduced average discharge times by 30%, from 8 hours to 5.6 hours. This improvement led to a 20% increase in positive patient feedback and helped the hospital handle an additional 1,000 patients annually, boosting overall operational capacity.
In the retail industry, Six Sigma has been effective in optimizing inventory management and reducing stockouts. A leading retail chain faced challenges with inventory turnover and frequent stockouts. By applying Six Sigma methodologies, including statistical analysis and process mapping, the retailer identified key issues such as inaccurate demand forecasting and supplier delays.
The implementation of improvements resulted in a 20% reduction in inventory holding costs and a 40% decrease in stockouts. This optimization not only improved product availability but also increased sales by $12 million annually, demonstrating the financial impact of effective inventory management.
Six Sigma has also made a significant impact in the financial services sector by improving transaction processing efficiency. A major bank applied Six Sigma to address delays and errors in its transaction processing system. By utilizing the DMAIC approach, the bank analyzed workflows and identified root causes of delays, including outdated systems and manual errors.
The improvements led to a 25% reduction in transaction processing time, from an average of 4 hours to 3 hours, and a 15% decrease in processing errors. These enhancements resulted in faster, more accurate transactions, increasing customer satisfaction and saving the bank approximately $10 million in operational costs.
In the telecommunications sector, Six Sigma has proven effective in improving customer service and reducing churn rates. A leading telecom provider faced high customer churn and frequent service complaints. By applying Six Sigma tools to analyze customer service processes, the company identified issues such as long wait times and service disruptions.
After implementing targeted improvements, the provider achieved a 15% reduction in customer churn rates, from 12% to 10.2%, and a 25% increase in customer satisfaction scores. These improvements not only enhanced customer retention but also contributed to an estimated $20 million increase in annual revenue due to higher customer loyalty and reduced service costs.
Six Sigma provides numerous benefits for operations management professionals, driving operational excellence and fostering a culture of continuous improvement. By implementing Six Sigma methodologies, professionals can achieve better process control, higher efficiency, and enhanced quality in their operations.
This approach helps in systematically identifying and addressing issues, leading to substantial gains in performance and organizational effectiveness. Here are the key benefits:
Six Sigma certifications are essential for professionals seeking to validate their expertise in process improvement and quality management. These certifications are tiered into various belt rankings, each representing a different level of proficiency and responsibility. From foundational knowledge to advanced problem-solving skills, Six Sigma belt rankings provide a structured path for career development.
Each belt signifies a professional’s ability to apply Six Sigma principles effectively and lead improvement projects. Achieving these certifications enhances a professional’s credibility and opens up new career opportunities in operations management and quality improvement.
Six Sigma certification and training are essential for professionals aiming to enhance their expertise in process improvement and quality management. These programs provide structured learning paths that cover various levels of Six Sigma methodology, from basic concepts to advanced strategies. Certification validates a professional’s ability to apply Six Sigma principles effectively in real-world scenarios.
Training programs are designed to equip individuals with the skills needed to lead projects, analyze data, and drive continuous improvement. Whether for career advancement or organizational development, Six Sigma certification and training offer valuable knowledge and credentials.
Six Sigma career paths offer diverse opportunities for professionals looking to advance in process improvement and quality management. In India, Six Sigma certifications open doors to roles across various industries, including manufacturing, finance, healthcare, and IT.
The demand for Six Sigma experts continues to grow as organizations seek to optimize operations and enhance efficiency. Salary prospects for Six Sigma professionals vary based on their experience, certification level, and industry. Here's a breakdown of key career options and their associated salary ranges in India:
Determining whether Six Sigma is the right fit for your company involves assessing several factors related to your operational needs and goals. Six Sigma is particularly beneficial for organizations aiming to enhance process efficiency, improve product quality, and reduce variability. If your company faces significant issues with process inefficiencies, high defect rates, or customer dissatisfaction, Six Sigma’s structured methodologies and data-driven approach can provide substantial improvements.
The methodology’s focus on identifying root causes, standardizing processes, and achieving measurable results makes it well-suited for companies seeking systematic, long-term solutions to operational challenges. However, Six Sigma requires a commitment to rigorous data analysis and a culture of continuous improvement, which might not align with every company’s current capabilities or strategic focus.
Implementing Six Sigma involves training staff, committing resources, and potentially reshaping existing processes. For smaller organizations or those with less complex operations, the investment in Six Sigma might outweigh the benefits. It’s crucial to evaluate whether your company’s size, industry, and specific operational challenges justify the adoption of Six Sigma and whether you have the resources to support its implementation effectively.
Six Sigma has proven to be a transformative approach in operations management, offering a robust framework for improving process efficiency and quality. By employing data-driven methodologies and a focus on reducing variability, Six Sigma helps organizations achieve higher levels of performance and customer satisfaction. Its structured approaches, such as DMAIC and DMADV, provide comprehensive tools for identifying the root causes of issues, implementing targeted solutions, and ensuring the long-term sustainability of improvements.
For companies aiming to optimize their operations, Six Sigma offers clear benefits, including enhanced process efficiency, improved quality control, and better decision-making based on statistical analysis. However, the successful implementation of Six Sigma requires a commitment to continuous improvement, adequate training, and a willingness to adapt existing processes. Organizations must assess their specific needs and resources to determine if Six Sigma aligns with their strategic goals. When applied correctly, Six Sigma can significantly drive operational excellence and contribute to sustained business success.
Copy and paste below code to page Head section
Six Sigma is a set of techniques and tools used for process improvement in operations management. It aims to identify and eliminate defects or variations in processes to improve overall quality and efficiency. By applying data-driven methodologies, Six Sigma seeks to achieve near-perfect performance, reducing the rate of defects to fewer than 3.4 per million opportunities.
Six Sigma improves process efficiency by employing the DMAIC (Define, Measure, Analyze, Improve, Control) framework to identify inefficiencies and implement targeted improvements. By analyzing data and using statistical methods, organizations can streamline workflows, reduce waste, and enhance performance. This leads to faster cycle times, lower costs, and more reliable outcomes.
The main Six Sigma methodologies are DMAIC and DMADV. DMAIC is used for improving existing processes, while DMADV focuses on designing new processes or products. DMAIC involves defining the problem, measuring performance, analyzing data, implementing improvements, and controlling processes. DMADV involves defining project goals, measuring customer needs, analyzing design options, designing the new process, and verifying that it meets the requirements.
Six Sigma certifications, including Green Belt, Black Belt, and Master Black Belt, validate a professional’s expertise in Six Sigma methodologies. These certifications can enhance career prospects, lead to higher earning potential, and open doors to advanced roles in process improvement. They also demonstrate a commitment to quality management and continuous improvement, making certified professionals valuable assets to organizations.
A company should assess its specific needs, goals, and current process challenges to determine if Six Sigma is suitable. Key factors include the need for process improvements, the complexity of existing workflows, and the organization's commitment to continuous improvement. Conducting a preliminary assessment or pilot project can help evaluate the potential benefits of Six Sigma before full-scale implementation.
Common challenges in implementing Six Sigma include resistance to change, inadequate training, lack of management support, and difficulty in maintaining momentum. Organizations must address these challenges by securing executive buy-in, investing in comprehensive training, and fostering a culture of continuous improvement. Effective communication and a clear plan for sustaining changes are crucial for overcoming these obstacles.