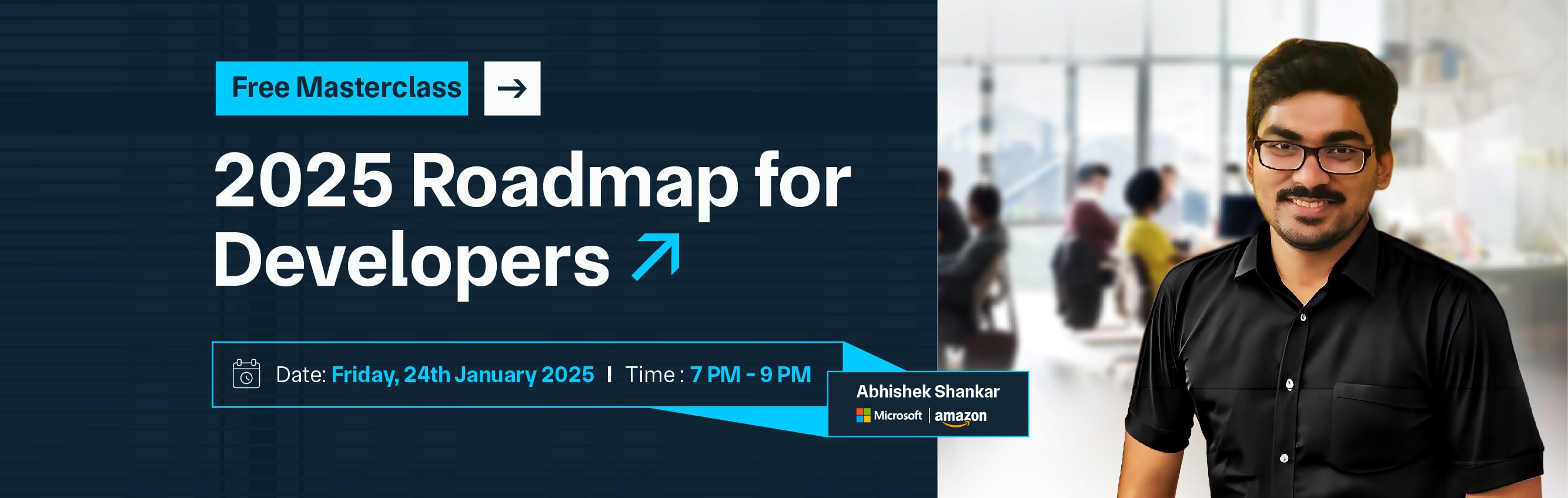
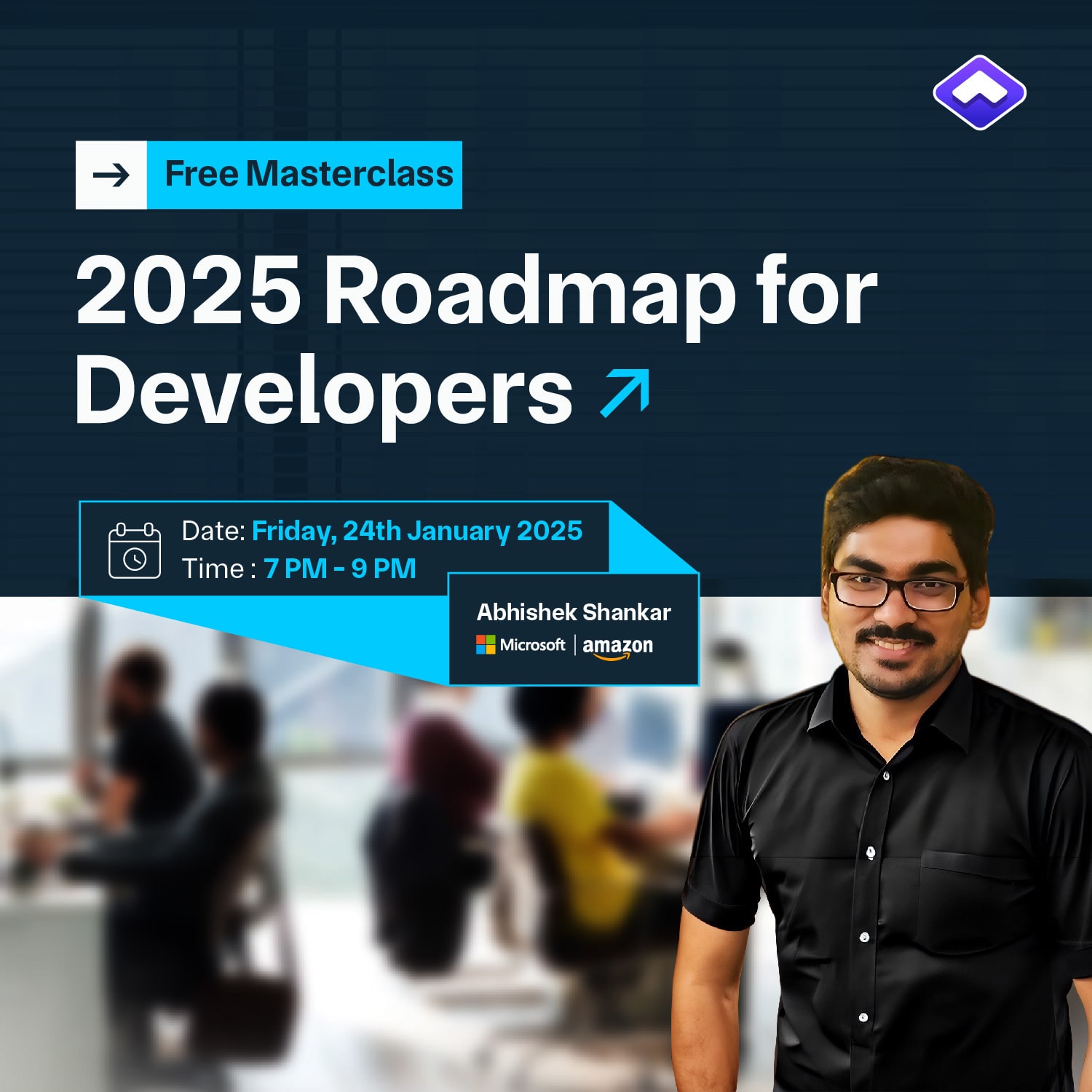
The Green Belt project focuses on creating sustainable urban spaces by incorporating nature and reducing environmental degradation. Key phases are involved in making the project successful, with planning, implementation, and maintenance being the most critical stages. These phases ensure the project addresses urban sprawl, enhances biodiversity, and promotes environmental awareness in urban areas. The planning phase is essential, as it sets the foundation for the project.
This stage includes environmental assessments, site selection, and understanding of the ecological impact. Identifying suitable tree species and creating a detailed planting plan are key tasks during this phase. Once planning is complete, the implementation phase begins. This stage involves executing the plan by clearing land, planting trees, and constructing paths and recreational spaces. It is crucial to ensure minimal environmental disruption and maintain the design’s integrity during this phase.
The final phase, maintenance, ensures the longevity and health of the Green Belt. Continuous efforts such as watering, pruning, and pest control help keep the plants thriving. Regular monitoring is essential to assess the success of the project and make necessary adjustments. These three phases planning, implementation, and maintenance work together to create a Green Belt that delivers long-term ecological, social, and environmental benefits.
A Green Belt project refers to the creation of designated areas of vegetation, typically forests or parks, around urban spaces to prevent urban sprawl, improve air quality, and promote biodiversity. These areas serve as natural barriers to limit the expansion of cities, providing a buffer zone between urban and rural landscapes. Green Belt projects also contribute to the aesthetic value of a region, offering recreational spaces for communities, as well as environmental benefits like reducing carbon emissions, protecting wildlife habitats, and improving overall ecosystem health.
In addition to environmental benefits, Green Belt projects play a crucial role in promoting sustainable urban planning. They are designed to provide long-term solutions for balancing urban development with nature preservation. These projects are often integrated into city planning strategies to create green corridors, improve public health, and support climate change mitigation efforts. With proper management and maintenance, Green Belt areas can become key resources for both ecological conservation and urban well-being, ensuring that cities remain livable and resilient in the face of rapid development.
A Green Belt project is a multi-phase initiative that requires careful planning, execution, and ongoing maintenance to achieve its objectives. These projects are designed to combat urban sprawl, promote sustainability, and protect local ecosystems.
The most crucial phases in a maximum Green Belt project are planning, implementation, and maintenance. Each of these phases plays a significant role in ensuring the project is successful and that its environmental, social, and economic benefits are realized in the long run. Below are the key phases involved in a Green Belt project.
The planning phase is the foundation of any Green Belt project. This stage involves identifying the best location for the green space, considering factors such as land availability, environmental impact, and proximity to urban areas. It also includes detailed assessments of the local ecosystem to ensure that the project supports biodiversity.
Urban planners and environmental experts collaborate to design a sustainable space, selecting the right tree species and determining how the land will be used for recreation, conservation, and educational purposes. Clear goals and a detailed strategy for achieving them are established during this phase.
Once the planning phase is complete, the implementation phase begins. This is the stage where the Green Belt project comes to life. It involves land preparation, such as clearing and leveling the soil and the planting of trees and shrubs. This phase also includes constructing pathways, recreational areas, and facilities for visitors.
A detailed implementation plan ensures that the project is carried out efficiently and with minimal disruption to the environment. During this phase, project teams must focus on adhering to the design and using sustainable practices to minimize the environmental footprint of the construction process.
The maintenance phase is crucial for ensuring the long-term success of a Green Belt project. It focuses on ongoing care and management of the green space to ensure that the plants, trees, and ecosystems continue to thrive. Regular activities include watering, pruning, pest control, and replanting where necessary.
Additionally, monitoring the health of the vegetation and the surrounding environment helps identify and address potential issues early on. This phase also involves educating the public about the importance of preserving the Green Belt and encouraging community involvement in the upkeep. Long-term sustainability is a priority, making continuous maintenance vital for the Green Belt to remain a valuable resource.
DMAIC is a structured, data-driven methodology used to improve processes by identifying and eliminating inefficiencies and defects. The acronym stands for Define, Measure, Analyze, Improve, and Control, representing the five key phases of the process improvement cycle. DMAIC is widely used in Six Sigma projects and is designed to help organizations enhance product quality, reduce process variations, and ultimately achieve better business performance. Each phase of DMAIC focuses on a specific objective, ensuring that all aspects of process improvement are systematically addressed.
In the Define phase, the project's goals, scope, and customer requirements are clearly outlined. The Measure phase involves collecting relevant data to establish a baseline for the current process performance. During the Analyze phase, this data is examined to identify root causes of inefficiencies or defects. The Improve phase focuses on implementing solutions to address the root causes and optimize the process. Finally, the Control phase ensures that the improvements are sustained over time through monitoring and ongoing process adjustments. By following these phases, organizations can continuously refine their processes and achieve long-term success.
DMAIC is a powerful methodology used for improving business processes by systematically addressing inefficiencies, defects, and variations. The process is data-driven and follows a structured approach that leads to more effective and sustainable improvements.
It is particularly useful in environments where consistent quality and performance are crucial, such as manufacturing and project management. DMAIC helps organizations achieve better outcomes by focusing on clear goals, data analysis, and continuous process monitoring. Below are key reasons why the DMAIC process is essential for businesses seeking continuous improvement.
The DMAIC methodology is a systematic, data-driven approach used for process improvement aimed at identifying and resolving inefficiencies. It consists of five phases: Define, Measure, Analyze, Improve, and Control. Each phase is designed to build upon the previous one, ensuring that issues are fully understood, solutions are data-driven, and improvements are sustainable. In the Define phase, the problem is clearly identified, and goals are set.
The Measure phase focuses on gathering data to understand current performance. In the Analyze phase, root causes are identified using data analysis. The Improve phase involves developing and implementing solutions to address the root causes, and the Control phase ensures that improvements are maintained over time. By following these phases, organizations can improve their processes in a structured and systematic way, ensuring lasting results and increased efficiency.
The Define phase is where the project begins, setting the stage for the entire improvement process. During this phase, the project goals, objectives, and scope are clearly defined, and the problem that needs to be solved is identified. A detailed project charter is created, outlining the resources, timeline, and stakeholders involved. This phase is critical because it ensures that everyone involved in the project understands the issue and the desired outcomes. Clear communication and alignment with key stakeholders are essential to the success of this phase.
Once the problem and goals are defined, the team identifies the customers’ needs and expectations to ensure that the project aligns with those requirements. This phase also involves defining the metrics that will be used to measure success throughout the project. These metrics, often referred to as Key Performance Indicators (KPIs), will serve as benchmarks to assess progress and determine whether the improvements made are effective. It is important to set a clear and measurable goal to avoid ambiguity and stay focused on the intended outcome.
In the Measure phase, the focus is on collecting data to assess the current performance of the process. This phase aims to establish a baseline, providing a reference point against which improvements can be measured. Data collection involves identifying the key variables that influence the process and measuring them accurately. It is essential to ensure the data collected is reliable and representative of the process's true performance. The team uses tools like process mapping and control charts to capture the performance data systematically.
Once the data is collected, it is analyzed to determine the extent of the problem and to identify areas of variation or inefficiency. This phase is crucial because it provides the factual evidence needed to understand the scope of the issue and set realistic targets for improvement. Accurate measurement helps establish a foundation for the rest of the DMAIC process, ensuring that the improvements made are based on actual performance data rather than assumptions or guesswork.
The Analyze phase is where the data collected during the Measure phase is carefully examined to identify the root causes of the problems or inefficiencies. This phase involves a deeper analysis of the data to understand patterns, relationships, and potential causes of defects or variations. Various statistical tools, such as regression analysis and Pareto charts, are used to analyze the data and pinpoint the factors that contribute most significantly to the problem.
The goal of this phase is not only to identify what is causing the issue but also to understand why it is occurring. By identifying the root causes, the team can ensure that solutions will address the underlying issues rather than just symptoms. A thorough analysis allows the team to prioritize the most impactful problems and focus on solving them, thereby ensuring that the improvements made will have the greatest positive effect on the process. This phase is essential for developing effective and targeted solutions.
The Improve phase focuses on developing and implementing solutions to address the root causes identified in the Analyze phase. This phase involves brainstorming and testing potential solutions to improve the process. Once the team has identified possible solutions, they are implemented through controlled experiments or pilot programs to assess their effectiveness before full-scale implementation. It is important to ensure that these improvements are feasible and sustainable over the long term. The goal is to optimize the process and eliminate inefficiencies.
During the Improve phase, the team works to refine the process and identify ways to standardize the improvements. It is essential to evaluate the impact of the changes through data to ensure that the solutions have had the desired effect. By improving processes based on the analysis of root causes, the team ensures that changes lead to measurable, positive outcomes. The improvements implemented should also be scalable, allowing for broader application if needed. This phase emphasizes experimentation and continuous refinement of the process.
The Control phase is the final phase of DMAIC, focusing on ensuring that the improvements made are sustained over time. This phase involves implementing monitoring systems to track the performance of the improved process and ensure that it remains stable. Control charts, process audits, and regular reviews are often used to monitor the process after the improvements have been implemented. This phase is critical for preventing process backsliding and ensuring that the improvements are maintained long-term.
In addition to monitoring, the Control phase involves creating a plan for ongoing process management. This includes establishing procedures for corrective actions in case performance deviates from the desired standards. The team documents the improvements made, standardizes best practices, and trains staff to follow the new processes. The goal is to institutionalize the improvements, making them a permanent part of the organization’s operations. By ensuring continuous monitoring and control, the team can guarantee that the changes made lead to sustained success.
DMADV is a structured methodology used primarily for designing new processes or products that meet customer expectations and deliver high-quality results. The acronym stands for Define, Measure, Analyze, Design, and Verify. It is commonly used when a project requires a complete redesign or when an existing process or product does not meet desired performance levels. Unlike DMAIC, which focuses on improving existing processes, DMADV is aimed at developing new processes from the ground up with a strong emphasis on customer needs, quality, and process optimization.
In the Define phase, the project goals, objectives, and customer requirements are clearly outlined. The Measure phase focuses on identifying the key metrics that will determine success. The Analyze phase involves understanding the relationship between process variables and customer requirements. In the Design phase, potential solutions or process designs are developed based on the analysis. In the Verify phase, the design is tested to ensure it meets customer expectations and can be effectively implemented. DMADV ensures that new products or processes are built with a focus on efficiency, quality, and alignment with customer needs.
DMADV is a methodology widely used for designing new processes, products, or services to meet customer expectations and quality standards. It is a structured approach that helps organizations ensure that their designs are both efficient and customer-centric. The acronym DMADV stands for Define, Measure, Analyze, Design, and Verify, and each of these phases plays a crucial role in achieving high-quality results. This methodology is often used when creating a completely new process or product or when redesigning one that doesn’t meet performance goals. Unlike DMAIC, which is applied to improve existing processes, DMADV focuses specifically on the creation of new solutions with a robust foundation grounded in data analysis and customer needs.
Each phase of DMADV has a distinct objective, and together, they ensure that the final design delivers not only high quality but also aligns with customer requirements. The Define phase sets the project scope and customer expectations. The Measure phase focuses on gathering data to understand key variables. The Analyze phase delves into root cause analysis to determine what influences customer needs. The Design phase develops and optimizes solutions, and finally, the Verify phase ensures that the design meets the desired goals before full implementation. By following these phases, organizations can systematically approach design challenges and deliver optimized, customer-aligned solutions.
The Define phase is the initial stage where the project's objectives, goals, and scope are clearly outlined. This phase focuses on understanding customer requirements and setting the expectations that the process or product must meet. A detailed project charter is created to highlight key deliverables, timelines, and resources. During this phase, it is essential to engage with stakeholders to ensure a shared understanding of the project’s purpose and expected outcomes. Defining the problem clearly at this stage reduces ambiguity and sets the foundation for all subsequent phases.
This phase also includes identifying the critical-to-quality (CTQ) elements that will guide the design process. CTQs are the attributes that customers find most important in a product or process, and aligning the project’s goals with these factors is crucial for success. By ensuring that customer needs are thoroughly understood and prioritized, the Define phase serves as the starting point for the entire DMADV methodology. Clear communication and agreement at this stage are vital for aligning all team members and stakeholders.
The Measure phase focuses on identifying key performance metrics and gathering relevant data to assess the current situation or requirements for the new design. This phase helps in understanding what needs to be measured in order to meet the customer’s expectations and ensures that the new design is built on solid data. The process includes identifying critical parameters, developing data collection plans, and ensuring the data is accurate and reliable.
In this phase, the project team uses statistical tools to gather and quantify data related to performance, customer needs, and other important factors. The data collected will serve as a baseline to measure the success of the design later on. The goal is to ensure that accurate data inform the design process and that potential problems or inefficiencies are identified early. This phase also lays the foundation for setting benchmarks, which will be used to evaluate the design’s performance in later stages of the project.
The Analyze phase involves a thorough evaluation of the data collected in the Measure phase. Here, the goal is to understand the relationships between different variables and how they influence the customer’s needs and expectations. Various analytical tools and techniques are used, including statistical analysis and process mapping, to identify patterns, trends, and root causes that will inform the design process. By analyzing the data, the project team can determine which factors have the greatest impact on customer satisfaction and the quality of the final product or process.
This phase is essential for prioritizing design decisions and ensuring that the most critical aspects are addressed in the subsequent design phase. The team also identifies potential risks and uncertainties that may affect the success of the design, enabling them to develop mitigation strategies early in the project. The insights gained during the Analyze phase ensure that the design is data-driven and aligned with the customer’s needs.
In the Design phase, the team develops potential solutions or designs based on the data and insights gathered during the previous phases. This phase focuses on creating a process or product that aligns with the customer’s requirements and meets performance targets. The team generates and evaluates multiple design alternatives, ensuring that they are feasible, cost-effective, and capable of delivering the desired outcomes. The design is refined through iterations, with continuous feedback loops to ensure it aligns with customer needs and project goals.
During this phase, various design tools such as simulation, prototyping, and design of experiments (DOE) are often used to test the different options and refine the design. It’s important to consider factors like ease of implementation, scalability, and long-term sustainability. The goal is to develop a solution that not only solves the problem but also optimizes performance and customer satisfaction. Design reviews and testing are key in ensuring that the best solution is selected and that the design process meets the highest standards.
The Verify phase ensures that the final design meets the customer’s expectations and performs as intended. In this phase, the team conducts tests, trials, and simulations to validate the effectiveness of the design. These tests help confirm that the new process or product performs according to the established metrics, quality standards, and customer needs. It is essential to validate the design before full-scale implementation to avoid costly mistakes or inefficiencies.
In addition to validating the performance, the Verify phase also includes ensuring that the design is sustainable and can be maintained over time. The team checks for long-term viability, scalability, and any potential areas of improvement. Any issues identified during the testing phase are addressed, and the final design is adjusted as necessary. Once the design passes verification, it is ready for full-scale implementation. This phase ensures that the design is not only functional but also effective and capable of delivering the intended benefits to the customer and organization.
DMAIC and DMADV are both structured methodologies used for process improvement and problem-solving, but they serve different purposes and are applied in distinct situations. DMAIC, which stands for Define, Measure, Analyze, Improve, and Control, is typically used for improving existing processes. It focuses on identifying inefficiencies, defects, or deviations and implementing solutions to optimize those processes. DMADV, on the other hand, stands for Define, Measure, Analyze, Design, and Verify and is used for designing new processes, products, or services.
DMADV is particularly useful when existing solutions cannot be improved further and require an entirely new approach to meet customer needs or performance goals. While both methodologies share similar phases, the key difference lies in their focus DMAIC targets the improvement of existing systems. In contrast, DMADV aims at creating new systems from scratch or when there is a need for complete redesigns.
DMAIC and DMADV are both crucial tools in process improvement, but they are used in different scenarios based on the specific needs of an organization. DMAIC is typically employed when there is an existing process, product, or service that needs optimization. It is ideal for addressing inefficiencies, defects, or variations in performance in processes that are already in place. DMAIC helps organizations improve quality, reduce costs, and enhance overall efficiency by refining the existing system. If the process is already functioning but underperforming or encountering issues, DMAIC is the go-to approach for incremental improvements.
On the other hand, DMADV is used when a completely new process, product, or service needs to be created or when a significant redesign is required. This methodology focuses on building solutions that meet customer needs from the very beginning. DMADV is suitable when an organization cannot make meaningful improvements to an existing process and requires a fresh approach to meet new performance or quality standards. It’s typically applied in situations like product development or the design of new business processes where the focus is on innovation and meeting specific customer requirements.
Green Belt projects are an essential part of Lean Six Sigma methodologies, typically aimed at improving efficiency, reducing waste, and enhancing processes within an organization. These projects are generally led by professionals who have completed Green Belt certification and work under the guidance of Black Belts or senior leaders.
Green Belt projects usually involve moderate complexity and focus on improving existing processes or systems. The goal is to apply data-driven decision-making to identify problems, analyze root causes, implement solutions, and ensure the improvements are sustained over time. Below are some examples of Green Belt projects that showcase how these professionals apply their skills to achieve tangible results.
One common Green Belt project involves identifying and eliminating defects in manufacturing processes. By using tools like the Pareto chart and root cause analysis, Green Belts works to detect areas in production that lead to high defect rates, such as equipment failure or process variation.
Once the root cause is found, improvements like changing machine settings, upgrading equipment, or streamlining workflows can be implemented. These changes help in reducing defects, increasing product quality, and improving customer satisfaction. By targeting specific defects, a Green Belt can significantly enhance production efficiency and reduce waste.
Inventory management is another area where Green Belt projects can make a substantial impact. Green Belts often tackle issues related to excess inventory, stockouts, or inefficient warehouse operations. Using DMAIC principles, they analyze the existing inventory system, measure performance, and identify areas where excess inventory is tying up capital or where stockouts are causing delays in production.
Solutions may include adjusting reorder points, improving demand forecasting, or implementing a just-in-time inventory system. By optimizing inventory management, organizations can reduce costs, improve cash flow, and enhance operational efficiency.
A Green Belt project can also focus on improving response times in customer service departments. This could involve identifying bottlenecks in communication, evaluating the existing response process, and finding ways to streamline operations. Techniques such as process mapping and time-motion studies may be employed to identify areas where delays occur, whether due to slow systems, under-trained staff, or inefficient workflows.
Once identified, solutions like automation, reorganization, or better staff training can be implemented to reduce response times. The result is a faster, more efficient customer service experience that increases customer satisfaction and loyalty.
Order fulfillment is another area often targeted by Green Belt projects. These projects aim to speed up the order-to-shipment process and improve accuracy. Green Belts analyzes the existing workflows, looking for delays or inconsistencies that slow down the fulfillment process.
For example, the time taken from order receipt to shipment can be reduced by optimizing routing, better inventory tracking, or improving communication between departments. The result is a quicker, more accurate fulfillment system that leads to satisfied customers and reduced operational costs.
In the healthcare sector, Green Belt projects often focus on improving patient flow through various departments, such as emergency rooms or outpatient services. Green Belt professionals use data analysis to pinpoint bottlenecks, delays, or inefficiencies that lead to long waiting times or overcrowding.
By implementing process improvements such as reorganizing patient intake systems, adjusting staffing schedules, or automating appointment scheduling, healthcare organizations can ensure that patients move through the system more efficiently. This not only improves patient satisfaction but also increases the overall capacity of the healthcare system to handle more patients without additional resources.
Green Belt projects in human resources often focus on improving employee training programs. These projects involve analyzing the current training process, identifying gaps in knowledge or skills, and designing improvements to make the training more effective.
For example, a Green Belt project might involve streamlining the training schedule to reduce downtime, improving training materials for better comprehension, or using technology to facilitate virtual learning. With optimized training programs, employees can become more efficient, reducing errors and increasing productivity in their roles.
A Green Belt project can also target energy consumption in manufacturing or office environments. By analyzing energy usage data, professionals can identify areas where energy is being wasted, such as inefficient machinery, poor insulation, or unnecessary lighting.
Solutions include upgrading equipment to more energy-efficient models, installing smart meters to track usage, or optimizing HVAC systems. These projects not only help to reduce operational costs but also contribute to sustainability goals by lowering the organization's carbon footprint and energy bills.
A Green Belt project aimed at improving supplier performance focuses on optimizing the supply chain by analyzing and addressing issues with suppliers. This may include delays in delivery, inconsistent quality, or poor communication. Green Belt professionals use tools such as supplier performance metrics, process mapping, and root cause analysis to identify areas of improvement.
Solutions could involve better supplier selection processes, improved communication channels, or renegotiation of delivery terms. By enhancing supplier performance, organizations can ensure smoother operations, reduce delays, and maintain consistent product quality, all of which lead to improved customer satisfaction and reduced operational disruptions.
Six Sigma Green Belt projects are designed to improve existing processes, reduce waste, and enhance overall efficiency. These projects typically focus on moderate complexity and require Green Belts to lead or participate in problem-solving efforts within their organizations.
Green Belts apply Six Sigma tools and techniques such as DMAIC (Define, Measure, Analyze, Improve, Control) to address process inefficiencies, reduce variation, and achieve measurable improvements. These projects are essential for organizations aiming to enhance quality, optimize resources, and meet customer expectations. Below are the key characteristics that define successful Six Sigma Green Belt projects.
Building a successful Green Belt project involves careful planning, clear communication, and the application of Six Sigma tools and methodologies. These projects are typically smaller in scope compared to Black Belt projects but require a focused approach to process improvement.
Green Belt professionals should ensure they clearly define project goals, involve relevant stakeholders, and utilize data-driven decision-making to guide improvements. Below are some essential tips to help you build successful Green Belt projects and achieve significant process improvements.
Six Sigma Green Belt Process Improvement refers to a structured approach used by organizations to improve business processes, reduce defects, and enhance overall performance. The Green Belt methodology is typically implemented by professionals who have undergone Six Sigma training and are proficient in using tools like DMAIC (Define, Measure, Analyze, Improve, Control). Green Belts focus on smaller-scale but significant process improvement projects that are aligned with organizational goals. Their role is to identify inefficiencies, apply data-driven strategies to solve problems, and ensure that improvements are sustainable over time. By using Six Sigma tools and techniques, Green Belts drive results that directly impact an organization’s bottom line, improving quality, reducing waste, and increasing customer satisfaction.
In the Six Sigma Green Belt process, professionals begin by defining the problem and gathering data to understand current performance. They then analyze the root causes of issues using statistical methods and process mapping. Once the causes are identified, improvements are made, and control measures are implemented to maintain those improvements in the long run. Green Belt projects focus on tangible outcomes such as improved efficiency, lower costs, or enhanced quality. The process not only leads to immediate benefits but also helps in creating a culture of continuous improvement within the organization.
Process improvement projects require the collaboration of individuals with diverse skills, expertise, and roles within an organization. People who work on these projects often include a mix of employees from different departments, each contributing their unique perspective to identify and solve problems.
The involvement of various stakeholders ensures that all aspects of the process are considered and that the solutions implemented are effective and sustainable. Below are some common types of individuals who work on process improvement projects.
Managing process improvements requires a cross-functional team, where different roles come together to streamline operations, reduce inefficiencies, and implement strategic changes. The management of these initiatives typically involves a collaborative approach, with key individuals such as Process Improvement Managers, Project Managers, Six Sigma professionals, and Team Leaders leading and executing projects. Process Improvement Managers are primarily responsible for overseeing the entire project, ensuring alignment with business goals, while Project Managers ensure the execution is on schedule and within budget. Six Sigma professionals, including Black Belts and Green Belts, use data-driven methodologies like DMAIC to analyze and optimize processes effectively.
In addition to project managers and improvement leaders, Quality Assurance Managers, Executive Sponsors, Change Management Professionals, and Data Analysts play significant roles. QA Managers ensure that the improved processes meet the required quality standards and regulatory requirements. Executive Sponsors offer strategic guidance and ensure sufficient resources, while Change Management Professionals help employees adjust to new workflows. Data Analysts gather and interpret data to assess the effectiveness of process changes. Each role brings unique expertise to the table, ensuring that the process improvement initiatives are well-planned, executed, and sustained.
Process improvement methodologies are integral to the success of Green Belt projects. These methodologies provide a structured approach to identifying inefficiencies, solving problems, and enhancing processes. A Green Belt professional uses various tools and techniques to analyze, design, and implement changes within an organization.
These methodologies help in identifying the root causes of issues, eliminating waste, improving quality, and increasing overall efficiency. Green Belt professionals, guided by frameworks such as Six Sigma, lean principles, and DMAIC, drive systematic improvements within the defined scope. By following a clear methodology, they ensure that changes are data-driven, sustainable, and aligned with business objectives. Here are some of the key methodologies that Green Belt professionals often use:
Six Sigma process improvement stands out from other methods due to its structured, data-driven approach focused on achieving high-quality results with minimal defects. It emphasizes using quantitative data to identify, measure, and eliminate variations within processes. Unlike some other improvement methodologies, Six Sigma specifically targets process defects and aims for 3.4 defects per million opportunities (DPMO) rate, making it a highly rigorous and result-oriented approach.
It also integrates well with other management and quality improvement frameworks, providing a comprehensive and systematic solution for process enhancement. Below are the key aspects that distinguish Six Sigma from other types of process improvement methods:
Process improvement is a critical element in achieving operational excellence, and Six Sigma Green Belt practitioners play an essential role in driving these improvements within an organization. To successfully implement Six Sigma methodologies, Green Belts must understand the core principles and tools involved in each stage of the process. They must be equipped to identify opportunities for improvement, analyze data effectively, and work collaboratively with team members to ensure project success. It’s also crucial for Green Belts to possess strong problem-solving skills, a keen eye for detail, and the ability to lead small teams towards impactful results.
Effective communication and a structured approach are the pillars of a successful Six Sigma Green Belt project. Green Belts should consistently evaluate the current state of processes, set clear goals, and implement measurable solutions. Understanding the DMAIC framework, using statistical tools for data analysis, and focusing on customer satisfaction will help Green Belts achieve process improvements that lead to greater efficiency and reduced waste. Additionally, fostering a culture of continuous improvement and encouraging team participation ensures long-term success in process optimization efforts.
In any Six Sigma Green Belt project, a clear and concise problem definition is the first and most important step. Defining the problem effectively ensures that you stay focused on what needs to be solved and allows the project to stay on track. A well-articulated problem statement guides the team and sets the direction for the project. Alongside this, setting specific, measurable, achievable, relevant, and time-bound (SMART) goals is essential for tracking progress and measuring success.
By having a clear problem definition, you create a shared understanding among the team, which fosters better collaboration and commitment to achieving the desired outcome. It also ensures that all stakeholders are aligned with the project’s goals and scope. Setting SMART goals helps in breaking down the process improvement into smaller, manageable objectives, and tracking them will give a sense of accomplishment and keep the team motivated as they move through the project stages.
A data-driven approach is the foundation of the Six Sigma methodology. Instead of relying on assumptions or anecdotal evidence, gather accurate data to identify the current state of the process. This data-driven decision-making allows you to pinpoint areas for improvement and uncover potential root causes of inefficiencies. Tools such as Pareto charts, histograms, and scatter plots are essential for analyzing the data and visualizing trends.
Data-driven insights ensure that the improvements you make are based on facts and not guesswork, increasing the likelihood of success. They help to identify patterns that would otherwise be difficult to detect. Additionally, data analytics allows you to prioritize issues based on their impact, ensuring that the most critical areas are addressed first. Regularly revisiting and analyzing the data throughout the project can also help you make timely adjustments and ensure that the process stays on track.
Involving key stakeholders early in the process ensures that everyone is aligned and that their expectations are met. Stakeholders, including process owners and team members, should be identified at the beginning of the project. Engage them by providing regular updates, seeking feedback, and incorporating their input into the project plan. Early involvement helps to secure buy-in and ensures that potential roadblocks are identified before they become significant issues.
By involving stakeholders in the decision-making process, you ensure that their perspectives are considered, which can lead to more effective solutions. It also helps you to manage expectations and avoid surprises later in the project. Stakeholder buy-in is crucial for the successful implementation and sustainability of the improvements. Regular communication with stakeholders builds trust and ensures that the project aligns with organizational goals and values, facilitating smoother execution.
Root cause analysis is one of the most important aspects of Six Sigma. The goal is not just to address the symptoms of the problem but to identify the underlying causes. Techniques like the 5 Whys, Fishbone diagrams, and Failure Modes and Effects Analysis (FMEA) are invaluable tools for uncovering root causes. These tools guide the team through the process of investigating and verifying each potential cause to identify the core issue.
By focusing on root cause analysis, you ensure that the solutions you implement target the real problems rather than just masking them. This helps to avoid recurrence and ensures that your improvements will have a lasting impact. Effective root cause analysis is crucial for sustainable process improvement. By taking the time to investigate and validate the causes thoroughly, you can make more informed decisions that solve the problem at its source, improving efficiency and effectiveness long-term.
Once the root causes have been identified, the next step is to develop and implement solutions. Solutions should be designed to eliminate the root causes and improve the process’s overall performance. As you implement these solutions, it’s crucial to standardize the best practices across the organization to ensure consistency and long-term sustainability. Documentation of procedures, training of employees, and clear communication are all part of ensuring that the changes are effectively incorporated into daily operations.
Standardizing solutions and best practices ensures that the improvements are maintained over time. It also helps reduce variation, making processes more predictable and easier to manage. Clear documentation provides a reference for current and future team members, ensuring continuity even after project completion. By embedding the changes into the organization’s culture and processes, you make the improvements a permanent part of how the organization operates, driving long-term success.
After implementing the solutions, continuous monitoring and control are essential to ensure that the improvements are sustained. Set up control systems such as control charts to track key performance indicators (KPIs) and identify any deviations from the new standard. Monitoring the process continuously helps to catch potential problems early before they escalate, allowing for corrective actions to be taken. Control measures also ensure that the improvements do not regress over time.
By regularly measuring performance and adjusting as necessary, you can ensure that the process remains optimized and that gains are maintained. In addition to tracking immediate results, continuous monitoring helps create a culture of continuous improvement, where ongoing adjustments are made to adapt to changing conditions or new challenges. This proactive approach helps to sustain high levels of performance and efficiency.
Collaboration is key to the success of any Six Sigma Green Belt project. Create an open and inclusive environment where team members feel encouraged to share ideas, challenge assumptions, and propose solutions. Team members should have diverse skill sets and perspectives, as this allows for more creative problem-solving and ensures that all aspects of the project are thoroughly examined. A collaborative environment enhances communication, fosters trust, and improves problem-solving capabilities.
Encouraging team members to work together helps break down silos and promotes cross-functional cooperation. Additionally, it ensures that every team member feels valued and contributes to the project’s success. This collaborative culture boosts morale, increases engagement, and helps drive the project forward, ensuring the best possible outcomes for the process improvement effort.
The DMAIC (Define, Measure, Analyze, Improve, Control) methodology is the core framework for Six Sigma Green Belt projects. By following DMAIC, you ensure that each phase of the project is completed in a structured and organized manner. In the Define phase, you identify the problem and set clear goals. During the Measure phase, you collect data to understand the current state. In Analyze, you investigate the root causes. The Improve phase focuses on implementing solutions, while Control ensures that improvements are sustained.
Using DMAIC provides a clear roadmap for process improvement, ensuring that no critical steps are skipped. This structured approach helps guide the team and makes the project more manageable. DMAIC also ensures that improvements are based on data and analysis, making them more effective and sustainable. By adhering to this methodology, you minimize the risk of errors and maximize the likelihood of project success.
The phases involved in a Green Belt project typically follow the DMAIC (Define, Measure, Analyze, Improve, Control) framework, which provides a structured approach to process improvement. By following these phases, Green Belt professionals can identify and address inefficiencies, ensuring that improvements are both effective and sustainable. The importance of each phase is clear: from defining the problem and measuring current performance to analyzing data, implementing solutions, and controlling the process for long-term success.
In essence, the phases of a Green Belt project are designed to ensure thoroughness and effectiveness. The approach emphasizes collaboration, data-driven decision-making, and continuous monitoring to guarantee that improvements are not only achieved but also maintained. Whether in manufacturing, healthcare, or service industries, these phases help Green Belt practitioners contribute to significant process improvements, driving overall operational excellence.
Copy and paste below code to page Head section
Six Sigma is a methodology aimed at improving processes by identifying and removing defects or inefficiencies. It uses statistical tools to analyze and improve processes, focusing on reducing variability to enhance performance, quality, and efficiency. Six Sigma projects follow defined steps to achieve measurable and sustainable improvements.
A Green Belt is a professional trained in Six Sigma principles and tools who leads smaller projects or assists in larger projects under the guidance of a Black Belt. They focus on process improvement and help teams identify issues, analyze data, and implement solutions to optimize processes in various areas of the business.
DMAIC stands for Define, Measure, Analyze, Improve, and Control. It’s a structured approach used in Six Sigma to improve existing processes. In this method, problems are defined, data is measured and analyzed, improvements are implemented, and controls are put in place to sustain the improvements and ensure long-term success.
The time it takes to become a Six Sigma Green Belt varies. Typically, it involves a certification course that can last anywhere from a few weeks to several months, depending on the depth of the program and the individual’s prior knowledge. The course includes both theory and practical application to ensure proficiency.
Six Sigma is applied across a wide range of industries, including manufacturing, healthcare, finance, telecommunications, and service industries. It is particularly effective in industries where process optimization, quality control, and efficiency are critical to success, helping organizations reduce waste, improve quality, and increase customer satisfaction.
Six Sigma projects use a variety of tools, including statistical process control (SPC), root cause analysis, Pareto charts, fishbone diagrams, and process mapping. These tools help Green Belts and Black Belts analyze data, identify defects, and implement improvements, all while following the DMAIC framework to achieve measurable results.